Regenerative Power Solutions for the Marine & Offshore Industry
Supporting the transition to DC Systems for sustainable marine operationsThe Role of Regenerative Power for Improved Efficiency
Regenerative power technology is revolutionizing the marine industry by significantly reducing operating and testing costs. This technology captures the kinetic energy generated during the start-stop cycles of mechanical equipment like hoists, cranes, and elevators, converting it back into electricity. This energy recovery process is particularly beneficial for systems that frequently start and stop, offering substantial cost savings.
EA Elektro-Automatik’s regenerative bidirectional power supplies are specifically designed for the marine industry’s unique testing needs, including photovoltaic inverters, backup batteries, and hybrid controls for submarines.
Related Products
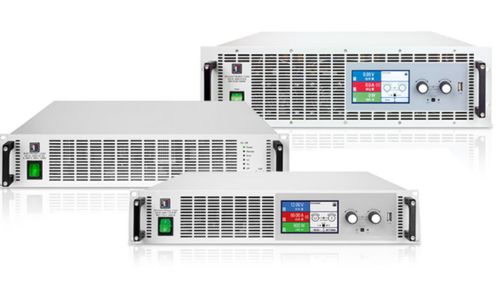
EL/ELR Regenerative & Conventional Electronic Loads
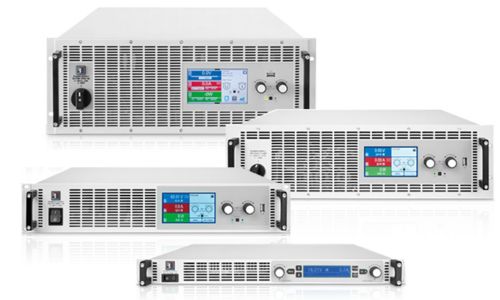
PSB Bidirectional DC Power Supplies
Why Partner with W5 Engineering?
Expertise
At W5 Engineering, we specialize in power electronics, providing unmatched knowledge of EA Powered products. Our team of technical sales engineers ensures you find the perfect solution for even the most complex requirements.
Custom Solutions
We deliver customized configurations and integrations tailored to your unique applications. Whether for R&D, production, or testing, W5 Engineering ensures your power systems meet exact specifications.
Rapid Shipping
With on-hand inventory and advanced logistics, we minimize lead times to keep your projects on track. Enjoy seamless delivery and peace of mind with our reliable shipping network.
Customer Support
Application Solutions
Electric Propulsion Systems: The Future of Sustainable Marine Transport
According to the United Nations Conference on Trade and Development, a staggering 80% of global commodities are transported by ships, a figure projected to rise by 3.8% annually. The downside? The majority of these vessels, including container ships, cruise liners, and oil tankers, rely on heavy diesel fuel, contributing significantly to environmental pollution. In total, the world’s 90,000 ships consume 370 million tons of fuel annually, emitting 20 million tons of sulfur oxide. The marine industry is thus under increasing pressure to adopt electric propulsion systems to mitigate these harmful emissions.
Types of Electric Drives in Marine Applications
Diesel-Electric Drive: This system utilizes diesel generators to produce electricity, which in turn powers electric engines responsible for propelling the ship.
Hybrid Drive: Incorporating on-board batteries and an internal combustion engine, the hybrid system can be activated briefly for power surges or to store excess energy. This allows the ship to operate solely on electric power for limited periods.
Fully Electric Drive: In this setup, the ship is entirely powered by batteries, eliminating the need for an internal combustion engine altogether.
By focusing on electric propulsion technologies, the marine industry is taking significant strides toward reducing its carbon footprint and promoting environmental sustainability.
EA Advantages
Impressed Cathodic Corrosion Protection: A Key to Marine Durability
ICCP Anode Configuration and Installation
The anodes used in ICCP systems are typically made from inert materials such as platinized titanium. These are strategically mounted on the exterior of the hull. To complete the circuit, cables from these anodes are channeled through the hull using a compression seal fitting, connecting to the positive terminal of the DC power supply. The negative terminal is then connected directly to the hull. These anodes are flush-mounted to minimize drag and are positioned at least 5 feet below the light load line to avoid mechanical damage.
Factors Influencing Anode Placement and Selection
The effectiveness of the ICCP system is influenced by the ship’s speed, dictating the current density needed for adequate hull protection. Special considerations are required for ships with mixed-material construction. For instance, vessels with aluminum hulls and steel fixtures can exacerbate corrosion due to the formation of an electrochemical cell. In such scenarios, aluminum or zinc galvanic anodes are employed to neutralize the potential difference between the two metals. Larger steel fixtures may necessitate the use of multiple anodes for effective corrosion protection.
By implementing ICCP systems, the marine industry can significantly extend the lifespan of vessels, thereby enhancing sustainability and reducing maintenance costs.
Magnetic Silencing Through Degaussing: Enhancing Stealth Capabilities in Marine Vessels
Steel-hulled ships essentially act as massive floating magnets. As they navigate through waters, their inherent magnetic fields interact with the Earth’s own magnetic field, either amplifying or diminishing its effects. This magnetic interference can inadvertently activate magnetic-sensitive ordnance or detection devices.
Importance of Degaussing Systems in Marine Safety
To mitigate this risk, marine engineers frequently incorporate degaussing systems into the ship’s design. These systems utilize degaussing coils through which electrical current flows, generating a counteractive magnetic field. This negates the magnetic disturbances caused by the ship’s movement, thereby reducing the likelihood of triggering magnetic-sensitive devices or ordnance.
Dynamic Adjustments for Global Navigation
The diagram below demonstrates how the activation of degaussing coils balances both the induced and permanent vertical components of the ship’s magnetic field, commonly referred to as the Z-zone. It’s crucial to dynamically adjust the coil current polarity as the ship transitions between hemispheres to maintain effective magnetic silencing.
By implementing advanced degaussing systems, ships can significantly improve their stealth capabilities, enhancing both safety and operational effectiveness in various naval scenarios.
Mitigating Risks of Sea Mines Through Magnetic Signature Management
Modern sea mines are increasingly sophisticated, capable of identifying a ship’s unique magnetic signature. When such a signature is detected, it can activate a torpedo or mine, providing both the location and type of vessel, primarily submarines.
Degaussing Systems: A Naval Security Solution
To counteract this maritime hazard, naval vessels often employ built-in degaussing (DG) systems. These systems effectively modify a ship’s magnetic signature, substantially lowering the risk of detection by sea mines.
By integrating advanced degaussing technology, naval forces can significantly enhance their stealth capabilities, thereby improving overall maritime security.
Future-Ready Electrified Submarines: Leveraging Siemens Marine's PEM Fuel Cells
Siemens Marine is revolutionizing the future of submarine propulsion with its Polymer Electrolyte Membrane (PEM) fuel cells. These cutting-edge fuel cells offer air-independent electric energy generation, requiring only hydrogen and oxygen as fuel sources.
Extended Dive Capabilities and Efficiency
By adopting PEM fuel cells, submarines can significantly prolong their underwater operational periods, outperforming traditional submarines that frequently need to surface for battery recharging. These innovative fuel cells not only enhance efficiency but also produce zero emissions.
Silent and Sustainable Operation
The electrochemical process of PEM fuel cells is not only eco-friendly but also silent, making it ideal for stealth missions. The byproducts are merely water and heat, further emphasizing its environmental benefits.
Longevity and Cost-Effectiveness
Designed for durability, these low-signature, nonmagnetic PEM fuel cells are built for long-term use. They come with an extensive service life and are supported by a cost-effective life cycle package, making them a sustainable choice for modern naval operations.
On-Shore Cathodic Protection: Custom Solutions for Jetties, Harbors, and Marine Structures
Cathodic protection isn’t just for ships; it’s also vital for safeguarding on-shore marine structures like jetties and harbors. Given the diverse structural geometries, compositions, and architectural designs, each structure demands a unique cathodic protection system.
Choice of Protection Systems
While galvanic anodes are commonly preferred, Impressed Current Cathodic Protection (ICCP) systems offer another effective option.
Expert Engineering Required
Due to the complexity and variety of marine structures, specialized engineering firms are often engaged to design custom cathodic protection solutions tailored to each structure’s unique needs.
Retrofitting for Enhanced Protection
In some cases, existing marine structures may require retroactive modifications to optimize their cathodic protection systems effectively.